RESTORATION
| Steel, stainless and aluminium works
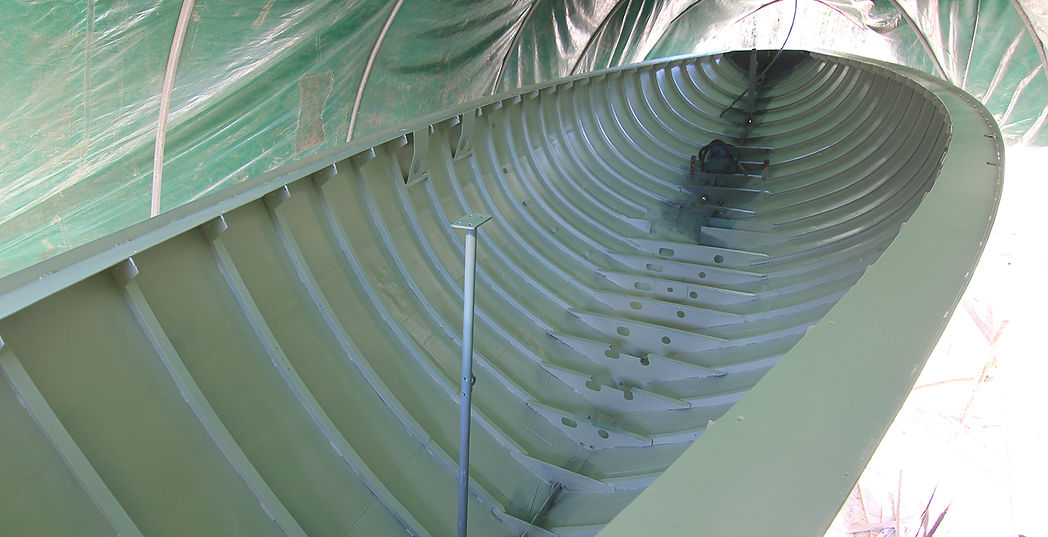
Photograph by Luísa Alpalhão
Vaz Moreira had commissioned a survey of Optimista’s steel hull where the areas with a thickness of 3mm, or less, where re-plated with new 4mm steel plates, to match the original thickness of the hull. However, as she was exposed to the weather for several years and water was seating in the bilges, further hull repairs had to be undertaken.
We started our restoration works by removing the superstructure and all auxiliary pieces to the hull. We undertook a comprehensive ultrasound survey of the hull's thickness under the waterline. Then, we thoroughly checked all of the hull below and above the waterline and made all necessary repairs to the steel work, including removal and re-fixing of the rudder stock tube, replacement of the trim tab stock tube and boss, placement of a new closed top cap over the keel. The original toenail had rusted away completely. To remain faithful to the original design, we welded a new strip of steel all around the hull which was then faired with epoxy filler to preserve the correct curvature of the hull.
New extra supports for the beams and half beams had to be fabricated and welded to the hull, as well as internal supports for the standing rigging.
We removed the old engine bed which was in poor quality and would have had to be replaced. Instead, we introduced a new steel structure in the bilge to accommodate the new electric engine and decided to weld fixed drainage tubes that would drain the water from the cockpit as structural elements both for the cockpit and companionway. The previous cockpit drainage system was overly complicated as it involved a complex system of pipes to divert the cockpit freshwater catchment into a tank.
Originally we designed and fabricated a stainless steel structure to support the two solar panels that would recharge the batteries. It was placed at the stern as an extension of the new pushpit. However, with time, we decided to remove the stainless structure as it compromised the boat’s design and performance and replaced the fixed solar panels with flexible lightweight movable ones which require no additional structure.
We fabricated new stainless steel stanchion poles and restored as many of the original stainless and brass fittings as possible.
Finally, we build two new aluminium lockers that fit under the berths in the saloon.
​